Intervju za „Pump engineer“ magazin
Throughout his career Mirko Vukcevic, Senior Maintenance and Development Engineer, has had the opportunity to work with a wide range of pumps and pump systems. His passion for engineering has led him to oversee a number of mega projects where he has gained significant knowledge and knowhow.
Pump Engineer Magazine had the pleasure of speaking with Vukcevic about his start in the pump industry, what he has learned from the projects he has worked on, and how he overcomes the challenges he has faced in the industry.
Mirko Vukcevic’s journey into the pump industry was quite unconventional. At 16 years old he began his career as a DJ playing music in European dance clubs and discos. “My love of music led me to DJ when I was young, and it was not until I was 30 that I realized I had a passion for engineering,” he said. After completing a degree in Mechanical Engineering from the University of Montenegro, Vukcevic started working in the water supply sector as a Technical Supervisor at a pump station in Podgorica, Montenegro.
“In my fourth year of study I chose to focus my training on pumps and pipelines which has remained my primary concentration for the past 11 years,” stated Vukcevic. “My focus on pumps in my final year of school was a huge advantage when I began working, as the company that hired me was in the process of reconstructing a main city pump station.
” Although he had the opportunity to work with experienced professionals on his first project, one of the biggest challenges Vukcevic faced at the onset of his career was the lack of internal mentors. “I felt particularly fortunate to work with Japanese partners on the pump reconstruction project, as they spent time mentoring me about the industry and I learned a great deal about pumps.As they had so much experience under their belts, I was able to ask them about anything and they would offer innovative solutions. Following the completion of the station, however I had very few other pump professionals who I could turn to for advice. This initially made getting familiar with all the applications difficult. Over time I became more comfortable and confident with the process I was working on, but I think the benefit of having an experienced person to guide you cannot be overrated.”
Working with Pumping Systems
Throughout his career, Vukcevic has had the opportunity to work closely with many types of pumps and pumping systems. While employed as a Technical Supervisor, he had the opportunity to work on a pump station reconstruction. This project was called “the urgent rehabilitation of Water Supply system in Podgorica” and called for the installation of 4 x 400 KW that pumped 400 liters per second. “For this project, we used a SCADA monitoring system, which allowed the pump to operate and be monitored on screens and computer systems. In a pump station, you must be careful and monitor every aspect of the plant, such as the temperature of gears, the concentration of chlorine, and the pressures of all the systems. Using SCADA system meant that we could monitor every aspect of the pump 24 hours a day.”
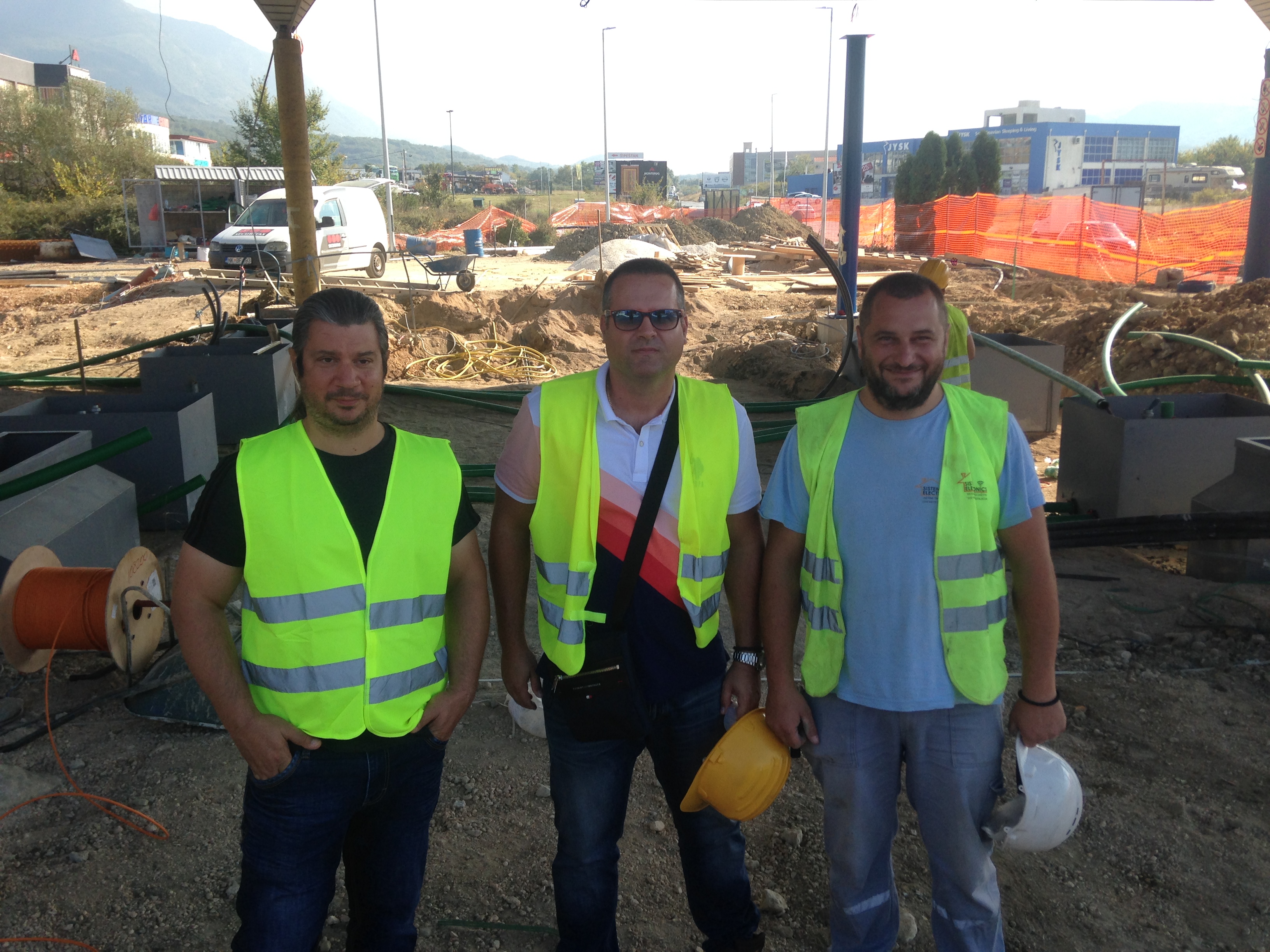
More recently, Vukcevic had the opportunity to work on a project with partners from Italy, where he oversaw the installation of a wastewater pump. “The pump we used for this particular project was 3 KW power and pumped groundwater from storm affected areas to a nearby river, at a rate of 40 liters per second. Due to the fragile nature of this particular site, it was essential that we remove the water as quickly as possible in order to mitigate the risk of it harming the surrounding environment,” he relayed. “In the last few years, we also completed reconstruction of seven petrol stations. When the water pressure at the stations is low, we are forced to use pumping booster sets with 2 pumps to increase the pressure, because we have 2 hydrants at each gas station.” The law requires that hydrants located at petrol site maintain a minimum pressure of 2.5 Bar. By adding pump to the hydrate system, the output pressure can be increased. These pumps also tend to have a variable frequency drives (VFDs) and need to carry a minimum of five to ten liters per second.
The Role of a Senior Maintenance and Development Engineer
For the last three years, Vukcevic has worked for Jugopetrol AD Podgorica, the biggest petroleum company in Montenegro, as the Senior Maintenance and Development Engineer, or Elephant Project Engineer. “Jugopetrol AD is part of the Hellenic Petroleum Group, which is the largest energy company in southeast Europe,” explained Vukcevic. “My principle role in this company is to oversee and supervise all of the jobs involved on the process side while also communicating with our external collaborates. As each project we work on requires different personnel and scope of labor, my day-today-day functions vary considerably. For example, today I had a call with a CEO of a water supply company to finish getting the pump station ready to operate. Tomorrow, I will be ensuring that we have all the necessary pipes to connect the water to a petrol station,” he continued.
Vukcevic is also responsible for sending weekly reports to the headquarters manager, as well as overseeing the various sites to ensure all of the projects are stayingon schedule. “Despite all of the driving, I feel very privileged to work for this company, because it gives me the opportunity to work with really knowledgeable and dedicated professionals,” stated Vukcevic. “I really
enjoy learning from the variety of professionals that are around me; we have a great team that brings about a very positive working environment.”
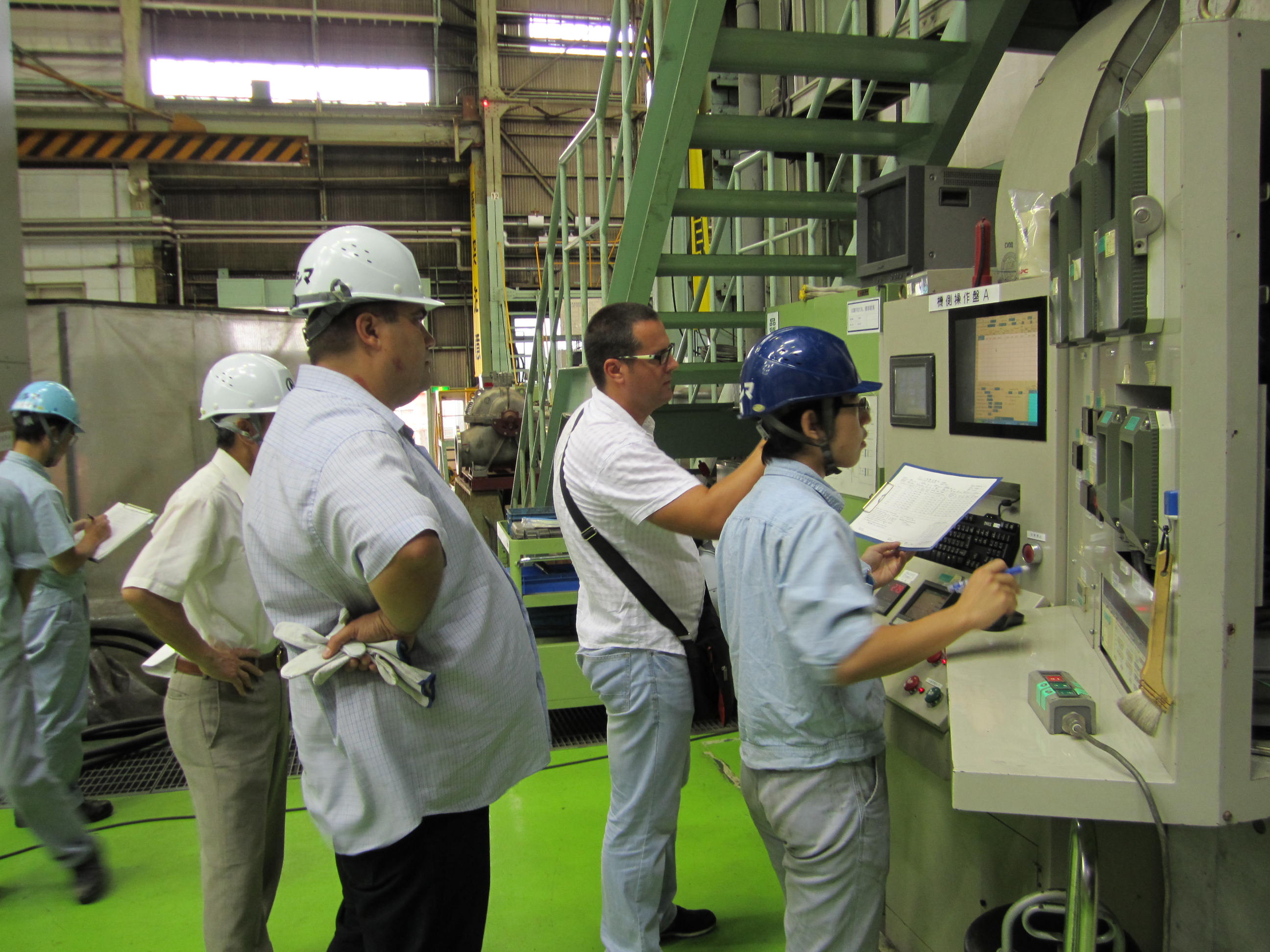
The most recent project that Vukcevic has undertaken in his role as an Elephant Project Engineer, is Jugopertol biggest to date, the Elephant Project. “The main focus is the reconstruction of a number of old petrol stations throughout Montenegro,” he relayed. “The company has 47 petrol stations, which is the equivalent of almost one in every city. We have finished almost 20, and are
starting to work on the others now.” Vukcevic considers this project to be quite difficult, because it requires the demolition of the station before working from the ground up. “We remove all the old fuel tanks and replace them with new fuel tanks with double sheet. This is in line with the new EU (European Union) standards. We also have to install new pipelines, which have a double sheet. Everything is new; the asphalt, concrete, fuel pipes, pipe pumps, fuel dispensers, etc. We work with pipe pumps a lot on this project, as they transfer fluid into the fuel dispensers, and each fuel dispenser has its own smaller pump.”
The most significant challenge with the Elephant project can be seen as somewhat unique.
Common Challenges
One of the most common problems with pumps in Montenegro has to do with electronics and electricity. “There are not typically many mechanical issues with the pumps. The issue is when the electricity shuts off and the pumps cannot run,” expressed Vukcevic. “Typically, 10% of the world’s energy and electronic consumption goes towards pumps alone. We have learned that if you have a correctly sized pump for your application, you can avoid a lot of issues with the consumption of energy. If you use a VFD, you have another great opportunity to save energy. With a VFD, you could save 50% to 60% of the amount of energy used, and it also reduces the maintenance costs by 25% to 30%. In the last five to ten years, VFDs have made significant progress and they increase the lifecycle of a pump as well.”
Vukcevic says there are many things that can be done to help with the electric issues, in terms of compensating for lost power. “However, as I am a Mechanical Engineer, I am not too familiar with those processes,” he admitted. “As far as I am aware, we have over-voltage protection that are put into the control panels of the pumps. The main focus/aim is to have a good control panel with lots of protection for the pumps. If you have a good control panel, you will have fewer issues with electricity.”
Another prominent challenge, in all of the projects Vukcevic has worked on, is unreliable lead times and waiting on external companies to provide their services. “We often work with national electric and water supply companies, and if they are not able to
provide service right away, it can cause huge delays to our projects,” he explained. As the procedural process can be very slow, which ultimately cost time and money, it is important to develop relationships with suppliers; good collaboration between companies is very helpful for completing a project.”
“I have a very strong connection with a company in Italy, and they are always reliable when it comes to the fast and efficient service and delivery of pumps. They have 5 factories all in one city and are therefore able to put together different elements of the pump quickly as they can draw from their various locations without having to wait,” he explained. “In the past, they have been able to deliver pumps in as few as five days, which is incredibly fast. Most companies suggest a six-toeight- week delivery time.”
Moving the Industry Forward
Having experienced firsthand the challenges of learning on his own, one of the ways that Vukcevic is giving back to the industry is by teaching the younger engineers around him. “I want to make sure that I am passing on my knowledge to the younger generation as I meet them. I know how tough it can be if you do not have someone to learn from,” he said. “It has been, however,
a little more difficult to do this recently because of COVID-19. Before the pandemic, I would get two orthree engineers together and we would spend the whole day driving from one site to the next, talking and sharing information. Now with COVID-19, we must travel and do things separately, which has made this process more difficult.”
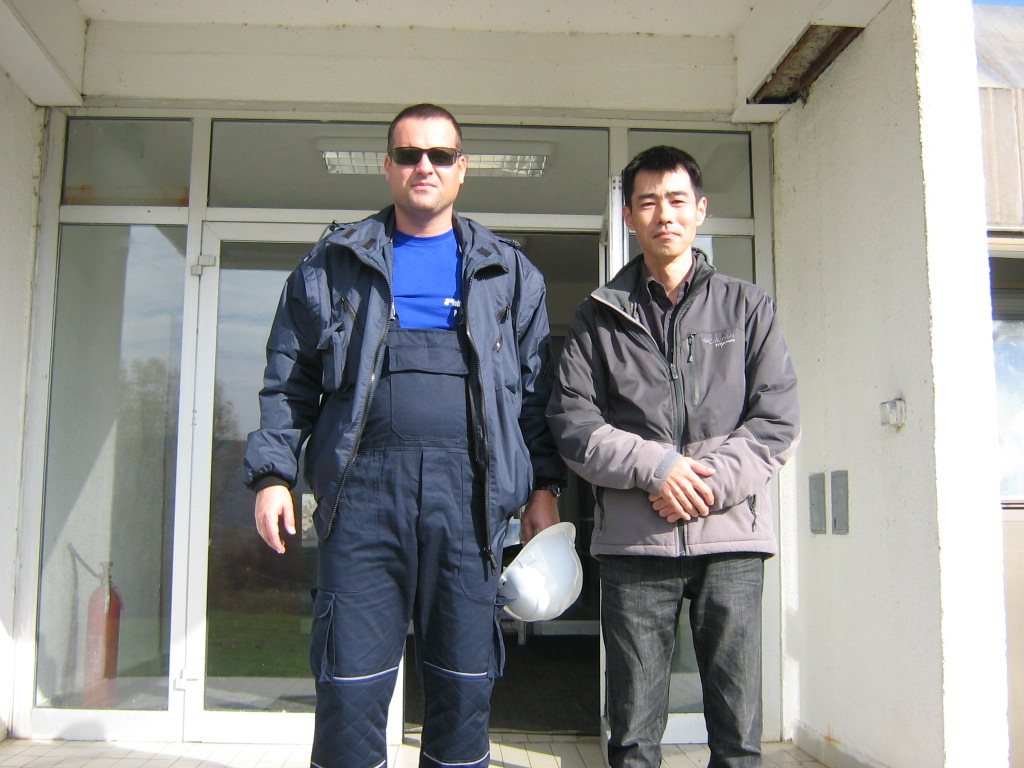
“We know that no matter what is going on in the world, pumps are always going to be needed to manage and distribute fluids, particularly water,” continued Vukcevic. “Water is one of the most needed resources in the world, and it must always be distributed. So no matter the challenge, whether it is COVID-19 or a lack of electricity, we need to make sure the pumps are working and the knowledge is being transferred.”
In order to keep the industry moving forward, Vukcevic hopes to see more people entering the pump industry. “I really enjoy this profession, and I hope more engineers are attracted to working with pumps in the future. I have made really good friends in this industry, and have been given the opportunity to travel and learn from various individuals with different backgrounds, and that is something I truly value.”
Izvor: „Pump Engineer“ magazin
Intervju za „Pump engineer“ magazin Read More »